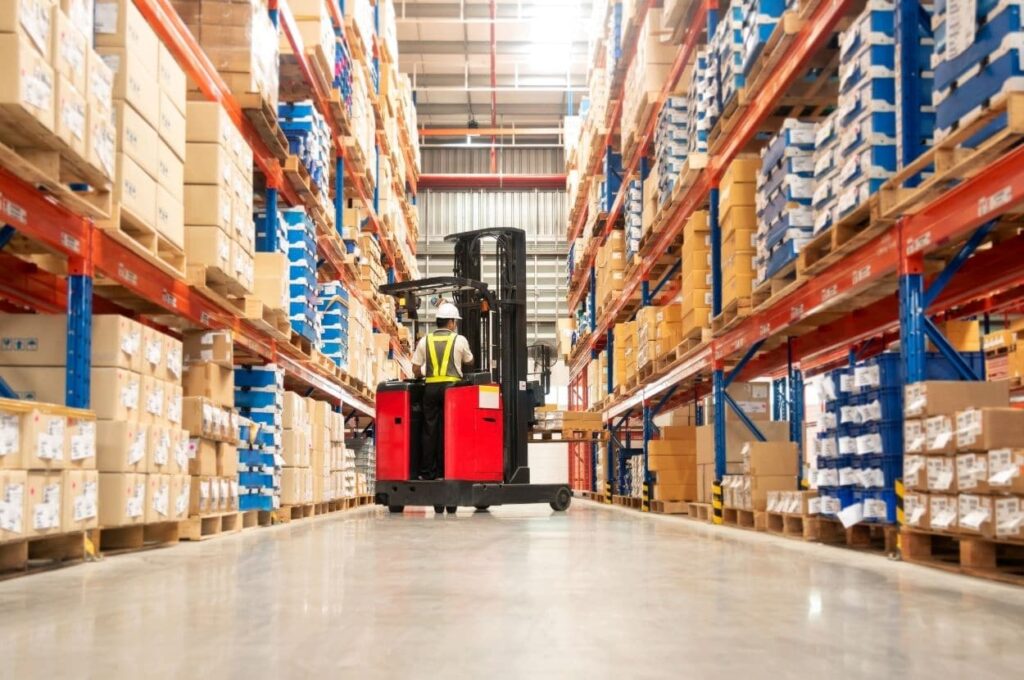
Being Dynamic in nature, Automotive Industry is one of the most volatile sector. This industry is complex and constantly endeavour to implement new technology. A single unit of car is manufactured by assembling of more than 15,000-20,000 small & big components. The management of such components is not easy. This requires planning, correct placement, proper labelling & correct packing. All these aspects are managed & supervised by the Warehousing Management team.
There are plethora of activities involved within the warehouse. In my opinion, there are two major movements namely inward & outward movement. Some of these include movement of items into the warehouse, maintenance of entries in the warehouse ledger, managing the shop floor pins, counting of the items, sorting and placement on its specified place, managing the shop floor bins and re-classification of warehousing items.
Out Activities incorporates outbound movement, counting, sorting and binning, transfer from warehouse to loading onto the vehicle with their serial / lot numbers along with outbound entry into the ledger to name a few. The items are required to be handled functionally & skilfully while managing cross decked and bulk items.
Whilst several tools have been put into implementation like Just in Time (JIT), Quality Management System (QMS) to eradicate the hiccups. QMS refers to policies & procedures which describe how the manufacturing
Unit manages & produces their end product. Whilst Just in Time refers to a method wherein goods are called by the manufacturer as & when required just before the production schedule reducing inventory pile up at factory to reduce holding cost & increase inventory turnover.
These technologies only improves process approach but also focuses on customer taste & preferences. Engagement of people strengthens relationship management amongst work force displaying their unity & leadership. Talking of long term benefits, it is mandatory for a company to adjust overall cost by various tools & methods whilst having profit as well.
However, warehousing is one wing which necessitates for planning, segregation, sorting, placement, timely movement and supply of goods to manufacturing unit.
There are several challenges in maintaining & managing automotive warehouses which handle huge volume of movement daily. On several occasions it has been observed that inventory is overstocked. The major challenge within the automobile industry has is to do with keeping inventories well-stocked but not overstocked. The demand of automotive and its supply are volatile in global marketplace. Different market has different taste & preference in Car, Motorcycle, Scooter etc. Therefore, the manufacturers have to find alternative ways to account for forecast in demand of its own goods & of competition. The automotive industry R&D section endlessly work for enhancing looks, shapes & upgradation of technology complicating the warehousing. In my opinion, an effective warehouse layout is extremely important as it directly impacts warehouse’s productivity and efficiency. Clarity in visualizing the inventory helps in understanding the stock maintained in the warehouse. Maintaining a level of consistency and error-proofing is pre-requisite to ensure that the right part gets to the right location just in time, every single time.
Secondly, due to huge volume of spare parts and accessories required, it is mandatory to arrange the stock as per size, nature & serial number. This unique Serial numbers are significant in tracking of the merchandise. Serial number tracking can account for all the information pertaining to its unique model, manufacturing date, Stock inward Date, expected date of expiry, where it needs to be placed, when and from whom it was purchased etc. Multiple quantities can be received and shipped through the functionality with lot and serial numbers from a single order detailed record. Through it, one can easily acquire detailed information about the transaction history of each item, and maintain all records that are required to trace an item while it is passed along the supply chain. Items from the vendor to the customer can also be tracked. All items can be handled by their functionality as well, and includes shipping cross-decked items and breaking bulk items. One may use it to pick document per order, or conduct a combination of different orders, and pick multiple orders in a single round depending on the manoeuvrability.
The working in warehouse isn’t just about lifting the boxes or driving a forklift. The management has much more to it as every employer heavily rely on the employees for management of physical goods. The automotive warehouse & supply chain is required to be much more organised, arranged as health and safety risks are associated with warehouse work. If you do not control them, the warehouse may face high employee turnover, underperforming workers, injuries and illnesses, missed workdays, legal issues, and at worst, fatalities. In most instances, Forklift safety is essential for preventing injuries. Therefore, the workforce must always wear Personal Protective Equipment (PPE) for work task, use proper tools for the work, not to work on live equipment, ensuring chemicals & adhesives are properly labelled and stored in their prescribed containers.
During the COVID-19 pandemic, a notable size of automotive industry responded supply chain disruptions as very significant. Due to high dependability on parts from OEM’s present in other parts of world, major automotive manufacturers could not complete vehicle assembly due to shortage. As a result, they had to put off long term plans and focus on immediate future. The supply chain were disruptive due to dearth of containers, vessel skipping the ports, reduced capacities of vessels & sky high freight rates. However, a leading logistics solution provider can assist automotive companies in resolving this supply chain issue. Having a cordial relationship with carrier, placement of special contract rates, special negotiation skills and a strong operations team can help to reduce the challenges being faced in supply chain.
A poor structure of warehouse can increase storage hurdles and a well laid, easily accessible & elaborated layout of the warehouse can be managed simply. The task can be simplified by grouping quick moving spare parts & segregating slower moving parts to less accessible warehouse location. This would help in refining operational efficiency & saving of time, energy & efforts. The term EWM refers to Extended Warehouse Management which has a technique to direct stock to the most effective warehouse location for storage. It also helps to decide the best fit suitable location segregating the goods by the packing & weight. Heavy & bulky parts can be stored on ground level whereas small & light weight parts can be arranged on upper shelves. Further, digital warehouses also facilitate proper layout, storage & binning of the cargo. Materials management is one of the biggest upcoming challenges in the automotive industry, as it requires excellent communication from all parts of the supply chain to ensure that warehouses receive the proper amount of inventory, control what inventory they do have, and find the most suitable solution to downsize current inventory. Automotive industry not only faces challenges in customer taste & preferences but also from its competitors.
In India, Gurugram & Manesar industrial hubs were prime place for automotive industry. However, Oragadam situated in outskirts of the port of Chennai is an emerging & fastest growing region for warehousing & automotive players.
Automotive Warehousing is not as easy as it seems to be. It is complex, ever changing, dynamic in nature which requires constant management since it involves series of activities with involvement of both men & machine. A well laid warehouse with advanced EVM system putting health & safety of people first can help in ease & effectiveness in production of the desired unit in automotive industry.