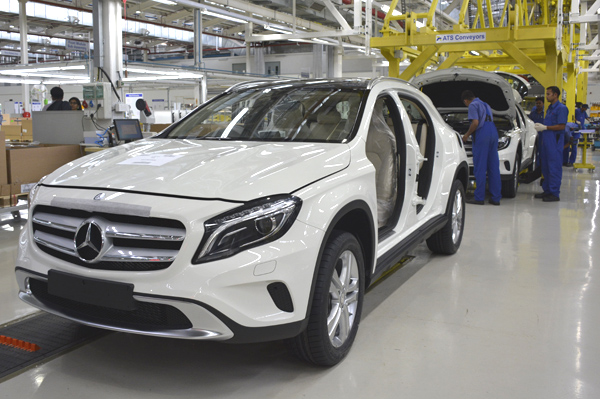
In contemporary times, we have multitudinous players in the market with diversified Automotive Supply Chain requirements. Each player has its unique approach in terms of vendor and material procurement (National or International level) and purchase criteria. This attributes for opportunities to manufacturers, traders & MSME’s to cater to their consumption patterns. In this context, Automotive Supply Chain contends to be fundamental & an essential part of the entire production chain.
Any final product is an amalgamation of several diversified units clubbed in the making, so is the case in Automotive Industry. In fact, Automotive Industry is one of the finest hi-tech, up-to-date and modernistic work area whereby Research & Development plays a pivotal role. This sector is ever-growing and ever-challenging too with stiff neck to neck competition in the market. Each component in the automotive sector is required either to be manufactured or to be sourced. For sourcing of material, the manufacturer has to rely on other suppliers, fabricators, raw material suppliers either internationally or in domestic market. Independent India witnessed several players approaching Indian market due to low cost rentals, efficient & cost effective resources. Suzuki which entered India in 1982 began its automotive production through India’s state owned manufacturer – Maruti Udyog. Its first manufactured car Maruti 800 turned out to be a super hit and became so popular that it used to be called as “People’s Car”.
As change is inevitable, this stimulates, thrills and brainstorms my analytical thinking without fear. Considering dynamism in nature, Logistics & Supply Chain business is ever-changing, vibrant, emphatic and fluctuating. Being a commander on PAN INDIA Basis, this dynamic characteristic enthrals my skills & ticks my conceptual nerves. Another alluring factor is my fancy towards automobiles which keeps me engrossed in this sector. Manufacturing, assembling, testing etc keeps me focused on new innovations being introduced. This gripped my interest & to pursue my passion I engrossed myself with several automotive giants in India. The automotive industry has been expanding at an appreciable pace amongst the emerging economies which have a major role in automotive supply chain.
Believe me, each day is a learning phase in both Automotive & its Supply Chain. In my professional tenure, have encountered some occasions wherein production posing line stoppage impacted entire supply chain activities. Such events require immediate attention and call of raw material in short span. This testifies my abilities to deliver the desired material prior to the deadline warned by the production team. These circumstances brought forth “Just in Time” commonly referred as “JIT” proverb in automotive sector.
Being cognizant of challenges in Automotive Supply Chain Management gave birth to several ideas to think up on areas of improvisation for effective supply of raw material & parts. I toured several automotive giant production units on PAN India basis & engaged their production, logistics & purchase teams to analyse their demand & supply patterns. This envisaged an insight to the possibility of disruption in supply chain process supporting me to make alterations with existing processes.
First & foremost, I established a missing connect between Purchase, Marketing, Logistics & Production team of the unit. Sales & Marketing force only focuses on selling the product however, they defaulted on timely deliveries. The delivery date promised by marketing department to end user was not pragmatic enough to ascertain the correct life cycle of shipment. Marketing team did not projected any kind delay in manufacturing at principal office with any vessel delay, if any. Further rains at port especially at Nhava Sheva delays railment of containers for desired ICD’s. Marketing team was given an in-depth knowledge on planning to sailing of goods to finally reaching of the material at factory. This session proved to reduce the rough & tumble relationship amongst inter-department. The result was fruitful as Supply Chain department was designated enough time to arrange planning to movement & delivery of cargo to production team.
Manufacturing in automotive industry is a herculean task as assembling of one Car is a combination of 15000 to 20000 components. It is beyond imagination for an auto manufacturer to manufacture such enormous components in-house. They are left with no choice but to outsource component manufacturers which demonstrates economic cost as well. The procurement is not only in the domestic market but internationally too. The international sourcing of component parts has become an industry standard mode of operation over many decades as OEMs and larger suppliers have sought to shop around the global market for parts and material inputs that meet necessary quality thresholds at the lowest cost. With my International travel & visit to various industrial houses, introduced many such OEM’s to some of major automotive manufacturers. This helped these units to procure quality material at reasonable cost with a streamlined automotive supply chain. Distances (and costs) for transportation and arrangements for warehousing are also a part of the picture, but higher efficiencies and technological advances in international freight shipping have underpinned phenomenal growth in international parts shipments.
Further, across the globe, international trade flows in automotive products – both finished vehicles and component parts is enormous. Companies like Toyota adopted Lean Manufacturing and this process works on principle of maximum production while minimising waste in manufacturing operations. This exercise helps in reducing operational cost, decreases lead time and enhances quality of the product. Having said that, I gave them a solution to procure material in bigger lots and avoid unnecessary transportation. Planning of production is required to map out in a manner to that ease of process wherein material require fitting. Supply Chain of bulk material shall reduce both packaging & shipping cost. This eliminates waste & dramatically impacts cost efficiency. The solution proved to be a blessing for some OEM’s I work with.
The International nature of the automotive supply chain became vulnerable to the Pandemic crisis and this sector was impacted adversely. Shortage of critical parts, lack of containers, vessels skipping their schedules meant knock on impact across the global automotive supply chain. Another major factor in disruption that automotive supply chain noticed was International Freight charges which were manifold times higher than actual prices. In this catastrophic situation, only those logistics service provider could survive who enjoyed strong and cordial relationships with carriers. For a Freight Forwarding organisation, it is utmost important to have healthy, friendly and professional connection with prime carriers & Co-loaders for smooth supply chain operations.
All these measures collectively indicate towards smooth, streamlined and short transit times with effective costings.